EDK Rotary Feeder


The Jeffrey Rader brand presents the innovative EDK Rotary Feeder/Delumper, meticulously engineered for the demanding needs of the plastics industry. This feeder is adept at precise volumetric feeding of polypropylene and polyethylene resin even under extreme pressures and temperatures. Featuring dual top knives for effective shearing, variable speed control, and anti-stall capabilities, it ensures uninterrupted operation in rugged applications. Its design incorporates advanced features such as a double-helical rotor with a labyrinth seal, adjustable end seals, and optional stainless-steel components. The feeder’s anti-jamming mechanism automatically reverses rotation to clear obstructions, guaranteeing continuous, efficient performance. With standard features like polished rotor surfaces to prevent material build-up and optional accessories including custom transitions and sight glasses, the EDK Rotary Feeder/Delumper offers unparalleled reliability and precision in material handling.
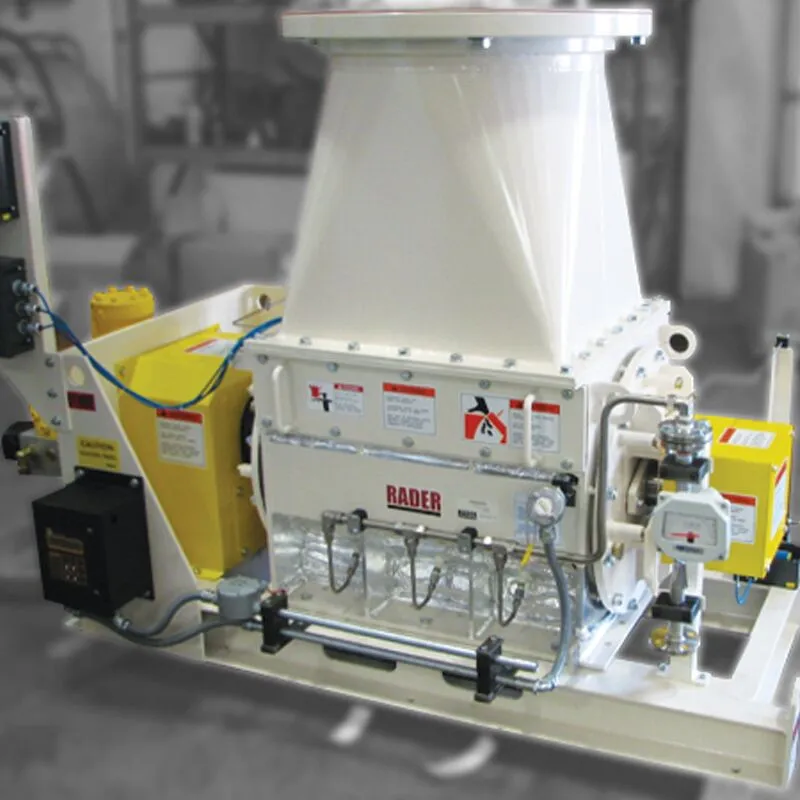
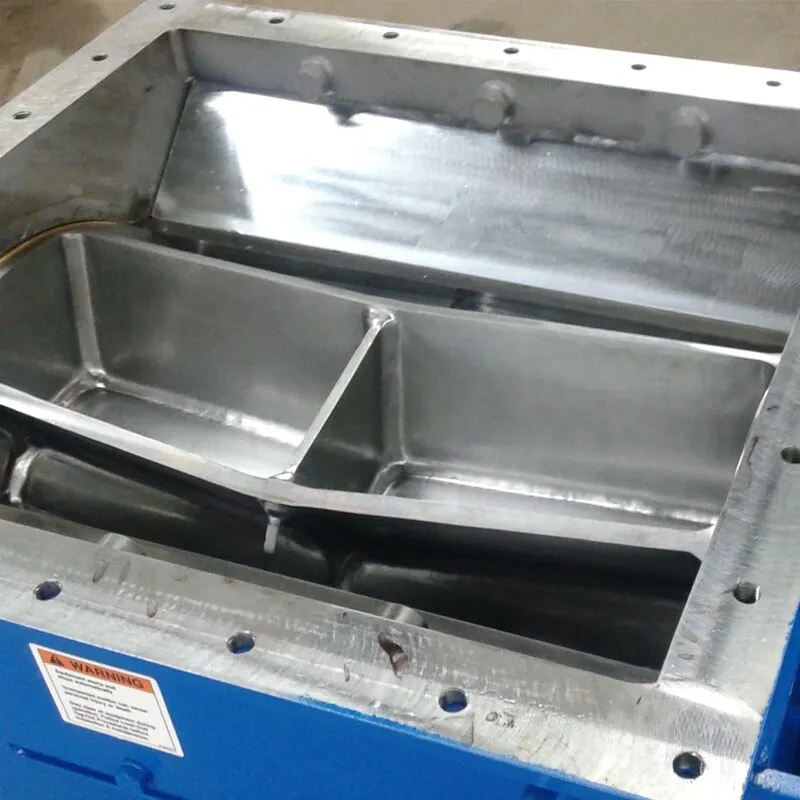
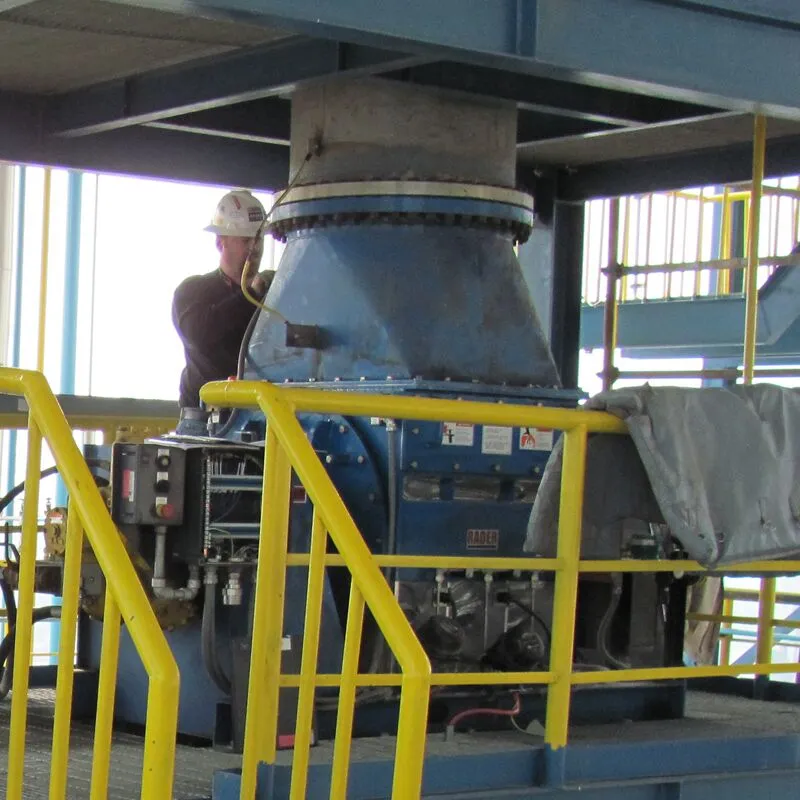
Features:
- Dual Top Knives: Equipped with dual top knives for shearing oversized materials in both rotation directions.
- Double-Helical Rotor: Features an eight-blade, closed-end rotor design with a two-blade labyrinth seal to minimize gas leakage.
- Special Rotor Tip Overlay: Rotor tips are overlaid with 410 stainless steel for enhanced durability and shearing efficiency.
- Adjustable End Seals: End seals are easily adjustable without removing the machine, ensuring convenience in maintenance.
- Heavy-Duty Outboard Bearings: Utilizes heavy-duty outboard bearings for robust operation and extended lifespan.
- High-Temperature Operation: Designed to operate at temperatures up to 230ºF (110°C), suitable for high-temperature applications.
- Anti-Jamming Feature: Automatically reverses rotation direction when encountering large lumps, with up to three attempts to shear the material.
- Stall Alarm: Alerts operators with an alarm in case of a stall condition, ensuring prompt attention to resolve issues.
Polished Rotor Surfaces: Rotor surfaces are polished to prevent material build-up, maintaining consistent performance.
Benefits:
- Precise Volumetric Feeding: Ensures precise volumetric feeding of polypropylene and polyethylene resin under high pressures and temperatures, enhancing operational efficiency.
- Rugged Construction: Built for heavy-duty service, providing reliability and durability in demanding industrial environments.
- Enhanced Safety: Incorporates OSHA protective guarding for safety compliance, ensuring a secure operational environment.
- Versatile Material Compatibility: Suitable for various materials including polypropylene and polyethylene resin, offering versatility in applications.
- Reduced Maintenance Downtime: Easy-to-adjust end seals and accessible maintenance features minimize downtime for maintenance tasks, optimizing operational productivity.
- Efficient Jam Clearing: Anti-jamming feature and automatic stall detection streamline the process of clearing jams, reducing downtime and enhancing operational efficiency.
- Customization Options: Offers a range of optional features such as housing materials, rotor configurations, and drive types, allowing customization to specific requirements.
- Material Compatibility: Compatible with both carbon steel and stainless steel construction, providing flexibility to meet different application needs.
- Consistent Performance: Precision engineering and high-quality materials ensure consistent and reliable performance over time, minimizing disruptions in production processes.
Features:
- Dual Top Knives: Equipped with dual top knives for shearing oversized materials in both rotation directions.
- Double-Helical Rotor: Features an eight-blade, closed-end rotor design with a two-blade labyrinth seal to minimize gas leakage.
- Special Rotor Tip Overlay: Rotor tips are overlaid with 410 stainless steel for enhanced durability and shearing efficiency.
- Adjustable End Seals: End seals are easily adjustable without removing the machine, ensuring convenience in maintenance.
- Heavy-Duty Outboard Bearings: Utilizes heavy-duty outboard bearings for robust operation and extended lifespan.
- High-Temperature Operation: Designed to operate at temperatures up to 230ºF (110°C), suitable for high-temperature applications.
- Anti-Jamming Feature: Automatically reverses rotation direction when encountering large lumps, with up to three attempts to shear the material.
- Stall Alarm: Alerts operators with an alarm in case of a stall condition, ensuring prompt attention to resolve issues.
Polished Rotor Surfaces: Rotor surfaces are polished to prevent material build-up, maintaining consistent performance.
Benefits:
- Precise Volumetric Feeding: Ensures precise volumetric feeding of polypropylene and polyethylene resin under high pressures and temperatures, enhancing operational efficiency.
- Rugged Construction: Built for heavy-duty service, providing reliability and durability in demanding industrial environments.
- Enhanced Safety: Incorporates OSHA protective guarding for safety compliance, ensuring a secure operational environment.
- Versatile Material Compatibility: Suitable for various materials including polypropylene and polyethylene resin, offering versatility in applications.
- Reduced Maintenance Downtime: Easy-to-adjust end seals and accessible maintenance features minimize downtime for maintenance tasks, optimizing operational productivity.
- Efficient Jam Clearing: Anti-jamming feature and automatic stall detection streamline the process of clearing jams, reducing downtime and enhancing operational efficiency.
- Customization Options: Offers a range of optional features such as housing materials, rotor configurations, and drive types, allowing customization to specific requirements.
- Material Compatibility: Compatible with both carbon steel and stainless steel construction, providing flexibility to meet different application needs.
- Consistent Performance: Precision engineering and high-quality materials ensure consistent and reliable performance over time, minimizing disruptions in production processes.
Technical Details
Standard Features
- Round inlet/outlet connections
- Carbon steel or stainless steel construction
- Special hard facing on rotor tips
- Outboard bearings
Knives and end seals adjustable - Shaft packing seals with nitrogen purge
- Polished rotor surfaces prevent material build-up
- Designed to operate at a differential pressure of 15 psi (1 bar) and at temperatures up to 230ºF (110°C)
- The maximum static differential pressure is 50 psi (3.4 bar)
- Rotor blades are ground to a RMS 16-22 finish
- Tips have 410 stainless steel overlay machined to match the rotor bore
Optional Features
Rotor
- Pocket dividers to limit piece size
- Reduced displacement
- Carbon steel or stainless steel
Drives
- Variable speed hydraulic
- Variable speed electromechanical
- OSHA protective guarding
Housing
- Chrome bore can be provided
- Carbon steel or stainless steel (housing and rotor to be the same materials of construction)
- Self-regulating heat tracing
Insulating blanket
Accessories
- Custom transitions
- Sight glasses
- Shaft seal purge regulator
- Pocket purge with regulator and timer
Standard Features
- Round inlet/outlet connections
- Carbon steel or stainless steel construction
- Special hard facing on rotor tips
- Outboard bearings
Knives and end seals adjustable - Shaft packing seals with nitrogen purge
- Polished rotor surfaces prevent material build-up
- Designed to operate at a differential pressure of 15 psi (1 bar) and at temperatures up to 230ºF (110°C)
- The maximum static differential pressure is 50 psi (3.4 bar)
- Rotor blades are ground to a RMS 16-22 finish
- Tips have 410 stainless steel overlay machined to match the rotor bore
Optional Features
Rotor
- Pocket dividers to limit piece size
- Reduced displacement
- Carbon steel or stainless steel
Drives
- Variable speed hydraulic
- Variable speed electromechanical
- OSHA protective guarding
Housing
- Chrome bore can be provided
- Carbon steel or stainless steel (housing and rotor to be the same materials of construction)
- Self-regulating heat tracing
Insulating blanket
Accessories
- Custom transitions
- Sight glasses
- Shaft seal purge regulator
- Pocket purge with regulator and timer