Electromagnetic Feeders

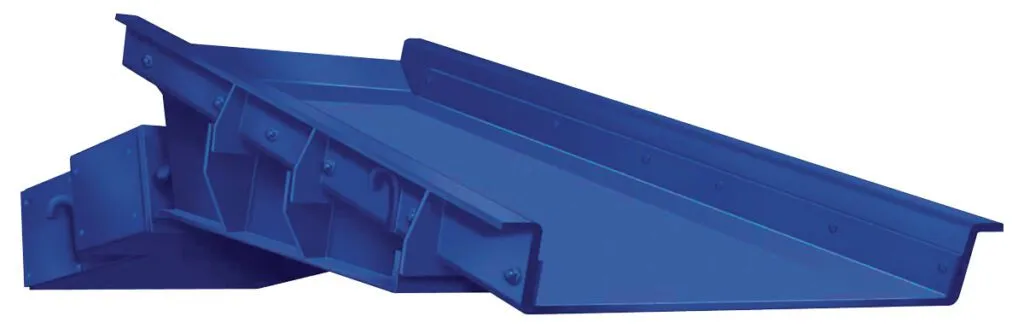
HP Electromagnetic
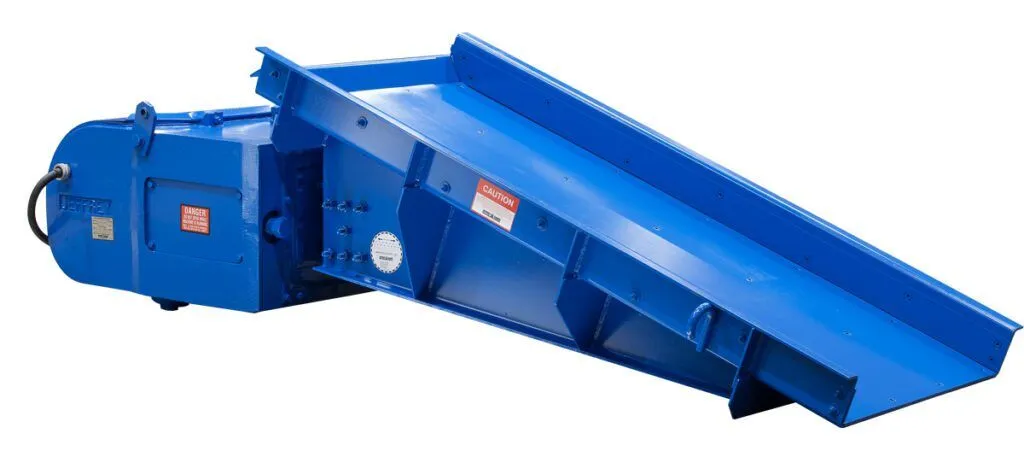
EF Electromagnetic
Jeffrey Rader’s EF and HP electromagnetic feeders use controlled, high-frequency vibration for efficient material handling across industries like aggregates, coal, minerals, and chemicals. With low maintenance and positive drive components, they offer reliable, quiet operation, reducing energy costs and ensuring long service life. These feeders feature sub-resonant tuning, vibration-absorbing springs, and NEMA 12-compliant controllers for precise control and soft starts. Their design flexibility, high reliability, and ease of maintenance make them ideal for various applications, delivering exceptional capacity and material control with components made in North America.
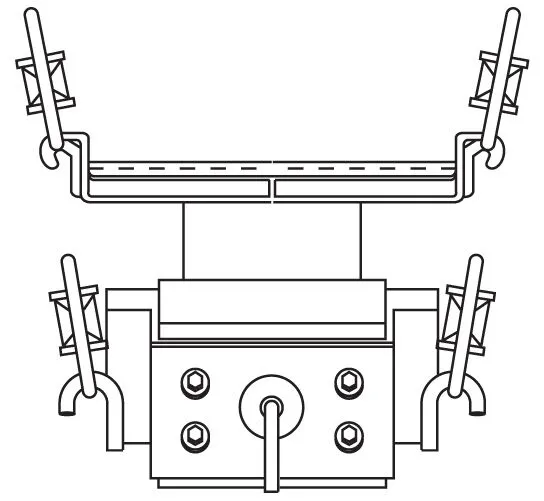
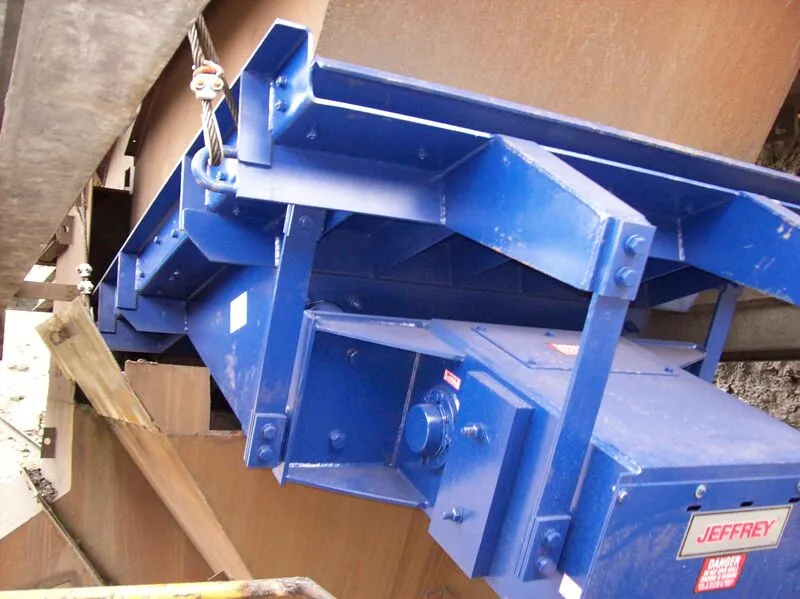
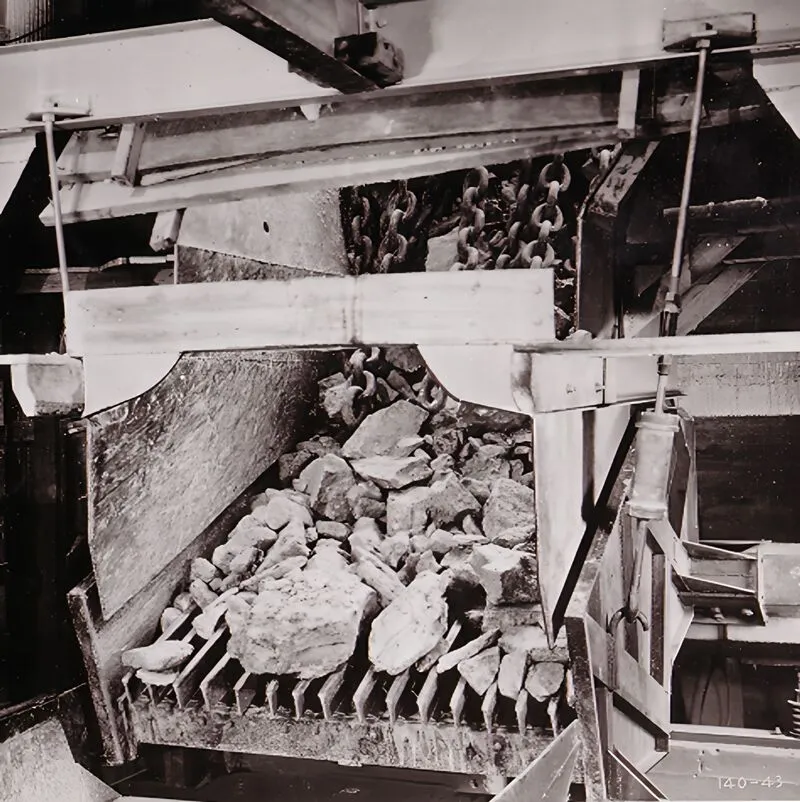
Features and Benefits
High-Frequency Vibration: Operates through controlled, high-frequency vibration. Efficient material movement and handling.
Low-Maintenance Design: Unique low-maintenance design. Reduces maintenance efforts and costs.
Positive Drive Components: Utilizes positive drive components. Ensures reliable and quiet operation while reducing energy costs.
Wide Range of Material Handling: Suitable for bulk material feeding of aggregates, coal, minerals, chemicals, industrial materials, and various blending materials. Versatile solution for diverse industrial applications.
Built for Longevity and Reliability: Built for long life and high reliability. Provides consistent, trouble-free service in various environments.
Customizable Design: Design flexibility, including open, enclosed, tubular, grizzly, and power unit overhead configurations. Accommodates specific application requirements with ease.
EF Model Features: Highest capacity for deck size in the industry. Maximizes material handling efficiency within limited space.
HP Model Features: Homogeneous core design with high flux density steel laminations. Delivers more tonnage per deck size compared to competitors.
Efficient Operation: Operates through sub-resonant tuning. Ensures efficient and continued feeder operation, even as liner wears.
Optimized Hopper Design: Recommended hopper design provided with each feeder. Facilitates correct deck loading, material flow, and continuous production.
Vibration Absorption: Equipped with vibration-absorbing spring assemblies. Reduces vibration transmission and enhances stability.
Precise Feeder Control: Electrical controllers designed for precise control. Enables accurate adjustment and monitoring of feeder performance.
Ease of Maintenance: No moving parts that require replacement. Simplifies maintenance procedures and lowers total cost of ownership.
North American Manufacture: All components made in North America. Ensures quality manufacturing standards and supports local industry.
Compliance and Certification: (CSA) approved controls available upon request.
Meets regulatory standards and enhances safety assurance.
High-Frequency Vibration: Operates through controlled, high-frequency vibration. Efficient material movement and handling.
Low-Maintenance Design: Unique low-maintenance design. Reduces maintenance efforts and costs.
Positive Drive Components: Utilizes positive drive components. Ensures reliable and quiet operation while reducing energy costs.
Wide Range of Material Handling: Suitable for bulk material feeding of aggregates, coal, minerals, chemicals, industrial materials, and various blending materials. Versatile solution for diverse industrial applications.
Built for Longevity and Reliability: Built for long life and high reliability. Provides consistent, trouble-free service in various environments.
Customizable Design: Design flexibility, including open, enclosed, tubular, grizzly, and power unit overhead configurations. Accommodates specific application requirements with ease.
EF Model Features: Highest capacity for deck size in the industry. Maximizes material handling efficiency within limited space.
HP Model Features: Homogeneous core design with high flux density steel laminations. Delivers more tonnage per deck size compared to competitors.
Efficient Operation: Operates through sub-resonant tuning. Ensures efficient and continued feeder operation, even as liner wears.
Optimized Hopper Design: Recommended hopper design provided with each feeder. Facilitates correct deck loading, material flow, and continuous production.
Vibration Absorption: Equipped with vibration-absorbing spring assemblies. Reduces vibration transmission and enhances stability.
Precise Feeder Control: Electrical controllers designed for precise control. Enables accurate adjustment and monitoring of feeder performance.
Ease of Maintenance: No moving parts that require replacement. Simplifies maintenance procedures and lowers total cost of ownership.
North American Manufacture: All components made in North America. Ensures quality manufacturing standards and supports local industry.
Compliance and Certification: (CSA) approved controls available upon request.
Meets regulatory standards and enhances safety assurance.
Industries
Agricultural/Food Processing • Biofuels & Pellets Production • Cement Production • Chemical Processing • Limestone & Lime Processing • Manufactured Products Preparation • Mining Operations (Aggregate, Sand & Gravel, Coal, Gypsum, Potash, and Other Minerals) • Petroleum Coke Processing • Power Generation • Waste Management
Agricultural/Food Processing • Biofuels & Pellets Production • Cement Production • Chemical Processing • Limestone & Lime Processing • Manufactured Products Preparation • Mining Operations (Aggregate, Sand & Gravel, Coal, Gypsum, Potash, and Other Minerals)
Petroleum Coke Processing • Power Generation • Waste Management
Agricultural/Food Processing • Biofuels & Pellets Production • Cement Production • Chemical Processing • Limestone & Lime Processing
Manufactured Products Preparation • Mining Operations (Aggregate, Sand & Gravel, Coal, Gypsum, Potash, and Other Minerals)
Petroleum Coke Processing • Power Generation • Waste Management