Posimetric Feeder
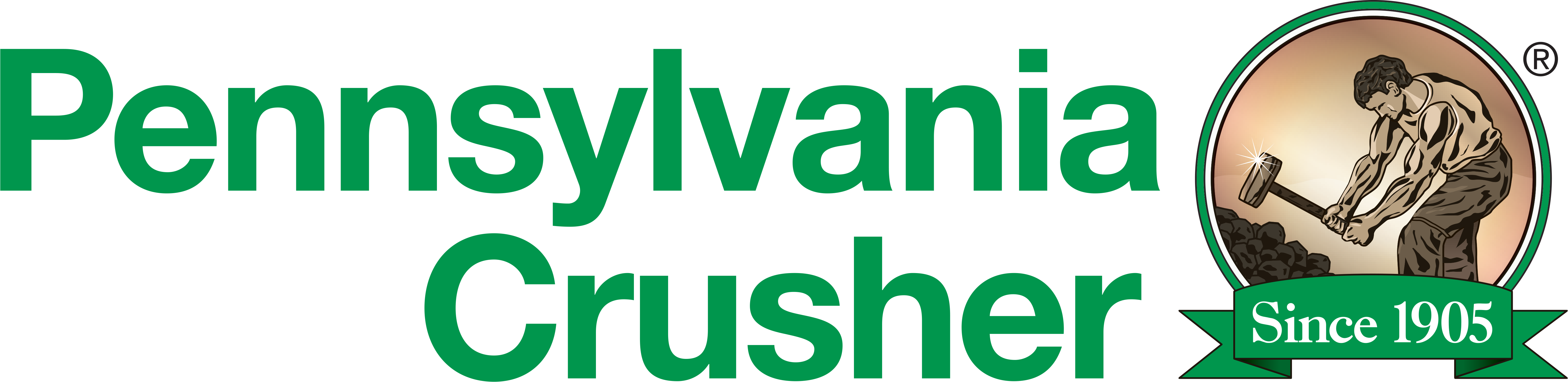

Introducing POSIFLOW™ Feeders by Pennsylvania Crusher Brand – a groundbreaking positive displacement feeder that revolutionizes feeding technology. These feeders offer unparalleled reliability, maintaining precise and constant feed rates with only a single moving part. Notably, they eliminate fugitive dust, enhancing safety in power plants and cement plants. POSIFLOW™ handles a wide range of bulk solid materials, from wet and dry to lumpy, sticky, abrasive, or granular, without feed rate errors due to moisture variations. With virtually no plugging, minimal downtime, and low maintenance requirements, this feeder simplifies operations and provides capacities from 3 to 1800 TPH. It’s a game-changer in uniform feeding, dust elimination, and trouble-free operation. POSIFLOW™ – where innovation meets efficiency!
Type L Disc Liners: Your Answer to Simplified Maintenance and Extended Equipment Life!
Our new Type L Disc liners for POSIFLOW™ feeders are designed to extend wear life and simplify rotor rebuilds. These liners tackle excessive wear on the rotor disc’s outside diameter, especially in abrasive material operations. With enhanced durability, they provide superior protection, reduce downtime, and cut maintenance complexities. Precisely aligned and securely fastened, they ensure long-term performance, slashing wear-part costs. Upgrade to Type L liners for improved POSIFLOW™ feeder performance and easier maintenance.

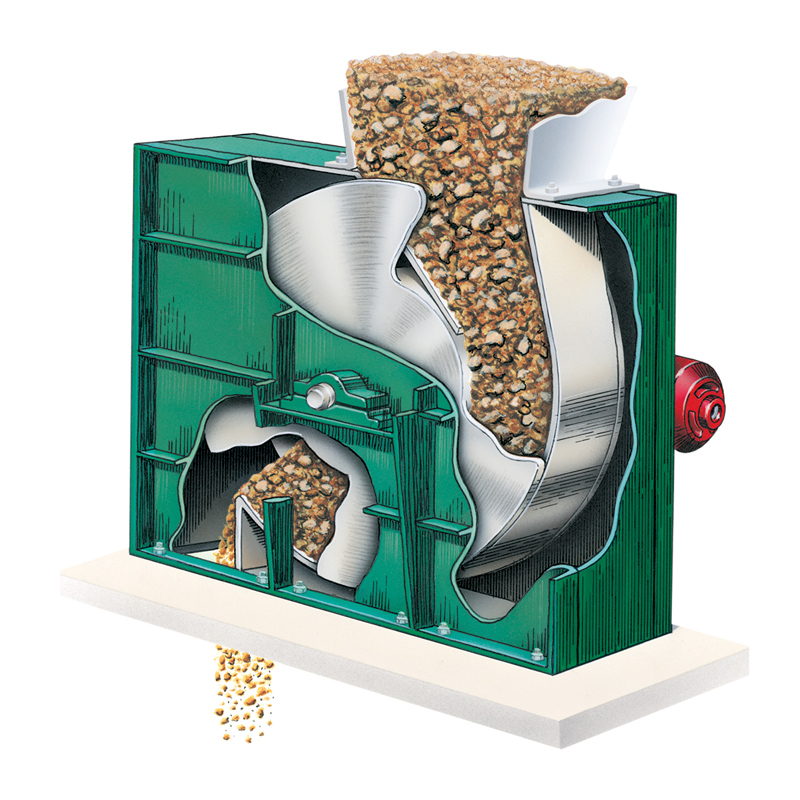

Features and Benefits:
Reliably Accurate and Constant Feed Rates: Maintains precise and constant feed rates, ensuring uniform feeding.
Single Moving Part: Operates with only a single moving part, reducing complexity and potential points of failure.
Fugitive Dust Elimination: Eliminates fugitive dust, enhancing safety in power plants and cement plants.
Wide Material Handling Range: Handles a wide range of bulk solid materials, including wet, dry, lumpy, sticky, abrasive, or granular materials.
Moisture Variations Tolerance: Not subject to feed rate errors from varying moisture levels in feed material, ensuring consistent performance.
Minimal Plugging and Downtime: Virtually eliminates plugging issues and reduces downtime, enhancing operational efficiency.
Low Maintenance Requirements: Requires minimal maintenance, with almost non-existent downtime for servicing.
Versatile Capacities: Provides capacities ranging from 3 to 1800 TPH, suitable for a wide range of applications.
Precise Material Control: Impossible to feed too little or too much material, ensuring accurate material delivery.
Energy-Efficient Operation: Operates at low rotation speeds and uses extremely low horsepower, optimizing energy usage.
Sealed Design: Seals against downstream suction or pressure, maintaining material flow control.
High Feed Rate Accuracy: Delivers up to 99.5% accuracy in feed rates, ensuring consistent processing.
Multi-Feeder Replacement: Replaces rotary, table, weigh feeders, and triple-gates with a uniform feed rate, simplifying equipment setups.
Improved Plant Safety: Dust-free operation improves plant safety and cleanliness.
Material Lock-Up Design: Utilizes controlled material lock-up for steady feed rates, reducing wear and ensuring reliable operation.
Gentle Material Handling: Carries material gently along the duct walls, minimizing wear and extending equipment lifespan.
Reliably Accurate and Constant Feed Rates: Maintains precise and constant feed rates, ensuring uniform feeding.
Single Moving Part: Operates with only a single moving part, reducing complexity and potential points of failure.
Fugitive Dust Elimination: Eliminates fugitive dust, enhancing safety in power plants and cement plants.
Wide Material Handling Range: Handles a wide range of bulk solid materials, including wet, dry, lumpy, sticky, abrasive, or granular materials.
Moisture Variations Tolerance: Not subject to feed rate errors from varying moisture levels in feed material, ensuring consistent performance.
Minimal Plugging and Downtime: Virtually eliminates plugging issues and reduces downtime, enhancing operational efficiency.
Low Maintenance Requirements: Requires minimal maintenance, with almost non-existent downtime for servicing.
Versatile Capacities: Provides capacities ranging from 3 to 1800 TPH, suitable for a wide range of applications.
Precise Material Control: Impossible to feed too little or too much material, ensuring accurate material delivery.
Energy-Efficient Operation: Operates at low rotation speeds and uses extremely low horsepower, optimizing energy usage.
Sealed Design: Seals against downstream suction or pressure, maintaining material flow control.
High Feed Rate Accuracy: Delivers up to 99.5% accuracy in feed rates, ensuring consistent processing.
Multi-Feeder Replacement: Replaces rotary, table, weigh feeders, and triple-gates with a uniform feed rate, simplifying equipment setups.
Improved Plant Safety: Dust-free operation improves plant safety and cleanliness.
Material Lock-Up Design: Utilizes controlled material lock-up for steady feed rates, reducing wear and ensuring reliable operation.
Gentle Material Handling: Carries material gently along the duct walls, minimizing wear and extending equipment lifespan.
Features and benefits of NEW Disc Liners for POSIFLOW™ Feeders:
Enhanced Wear Life: The Type L disc liners significantly extend the wear life of POSIFLOW™ feeders, especially on highly abrasive materials.
Simplified Rotor Rebuilds: These liners simplify the process of rebuilding the POSIFLOW™ rotor by providing additional protection to the OD surfaces of disc plates.
Increased Durability: The liners add extra protection to the POSIFLOW™, improving its performance and extending the wear life of its OD surfaces.
Secure Attachment: Type L liners are securely fastened to the discs using flat-head, countersunk machine screws during retrofit or rebuild, ensuring precise alignment and long-term performance.
Maintenance Benefits: The improved wear protection offered by Type L liners leads to reduced downtime, simplified maintenance, and long-term reduction in wear-part costs.
Improved Performance: Enhanced durability and wear resistance result in improved performance, especially when processing abrasive materials.
Cost Savings: Extended wear life and simplified maintenance contribute to long-term cost savings for customers.
Reduced Downtime: The increased durability and easier maintenance translate to reduced downtime and increased operational efficiency.
Ease of Rebuilds: Simplified rotor rebuilds make maintenance tasks more manageable and less time-consuming for maintenance teams.
Enhanced Equipment Longevity: By protecting the OD surfaces of disc plates, the Type L liners help prolong the overall longevity and reliability of POSIFLOW™ feeders.
Enhanced Wear Life: The Type L disc liners significantly extend the wear life of POSIFLOW™ feeders, especially on highly abrasive materials.
Simplified Rotor Rebuilds: These liners simplify the process of rebuilding the POSIFLOW™ rotor by providing additional protection to the OD surfaces of disc plates.
Increased Durability: The liners add extra protection to the POSIFLOW™, improving its performance and extending the wear life of its OD surfaces.
Secure Attachment: Type L liners are securely fastened to the discs using flat-head, countersunk machine screws during retrofit or rebuild, ensuring precise alignment and long-term performance.
Maintenance Benefits: The improved wear protection offered by Type L liners leads to reduced downtime, simplified maintenance, and long-term reduction in wear-part costs.
Improved Performance: Enhanced durability and wear resistance result in improved performance, especially when processing abrasive materials.
Cost Savings: Extended wear life and simplified maintenance contribute to long-term cost savings for customers.
Reduced Downtime: The increased durability and easier maintenance translate to reduced downtime and increased operational efficiency.
Ease of Rebuilds: Simplified rotor rebuilds make maintenance tasks more manageable and less time-consuming for maintenance teams.
Enhanced Equipment Longevity: By protecting the OD surfaces of disc plates, the Type L liners help prolong the overall longevity and reliability of POSIFLOW™ feeders.
Industries
Cement Production • Chemical Processing • Limestone & Lime Processing • Mining Operations (Coal, Gypsum, Potash, and Other Minerals)
Petroleum Coke Processing • Power Generation • Steel Production • Waste Management
Technical Details
Frame: ASTM A36 Fabricated Steel Plate
Upper Glide Plate: ASTM A36 Fabricated Steel Plate (surface: Type 304 Stainless Steel)
Lower Glide Plate: ASTM A36 Fabricated Steel Plate (surface: Type 304 Stainless Steel)
Abutment Weldment: ASTM A36 Fabricated Steel Plate
Outer Shroud Plate: UHMW Polyethylene
Inner Shroud Plate: Type 304 Stainless Steel
Shaft Seals: STYLE #1600 FLAX
Rotor Shaft: ASTM A567, GRADE 1141 Hot Wrought Steel
Rotor Discs: ASTM A514-70, GRADE B, “T-1” TYPE “A” Alloy Steel
Rotor Hub: Mechanical Tubing or Steel Pipe
Abutment Plates: Type 304-L Stainless Steel
Bearings: Self Aligning Anti-friction Roller Bearing
Standard Lubrication is Grease
Frame: ASTM A36 Fabricated Steel Plate
Upper Glide Plate: ASTM A36 Fabricated Steel Plate (surface: Type 304 Stainless Steel)
Lower Glide Plate: ASTM A36 Fabricated Steel Plate (surface: Type 304 Stainless Steel)
Abutment Weldment: ASTM A36 Fabricated Steel Plate
Outer Shroud Plate: UHMW Polyethylene
Inner Shroud Plate: Type 304 Stainless Steel
Shaft Seals: STYLE #1600 FLAX
Rotor Shaft: ASTM A567, GRADE 1141 Hot Wrought Steel
Rotor Discs: ASTM A514-70, GRADE B, “T-1” TYPE “A” Alloy Steel
Rotor Hub: Mechanical Tubing or Steel Pipe
Abutment Plates: Type 304-L Stainless Steel
Bearings: Self Aligning Anti-friction Roller Bearing
Standard Lubrication is Grease
