DynaGage™ Bar Screen

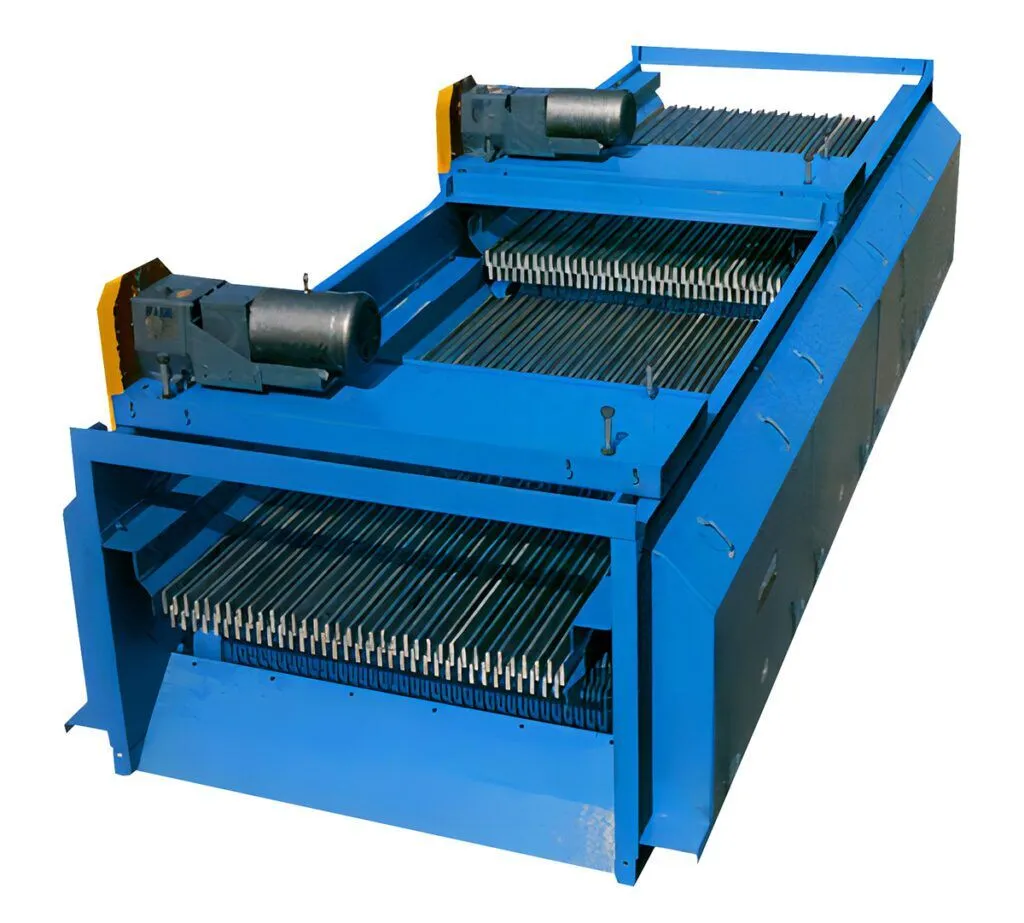
Jeffrey Rader’s DynaGage™ Bar Screen revolutionizes chip screening with unmatched efficiency, offering over 90% separation efficiency and minimal accept carryover. This technologically advanced screening solution eliminates the need for costly maintenance and replacement of screening surfaces, resulting in extended performance life. Its unique oscillating Gagebars™ action optimizes material passage, while the absence of rotating wear surfaces reduces energy consumption and space requirements. Whether for new screen rooms or existing operations, the DynaGage™ provides cost-effective installation and operation, with low horsepower requirements for high throughput, translating to significant energy savings. It’s the ultimate choice for enhanced selectivity, greater flow-rate control, and reduced operating expenses in wood yard operations and woody biomass processing.
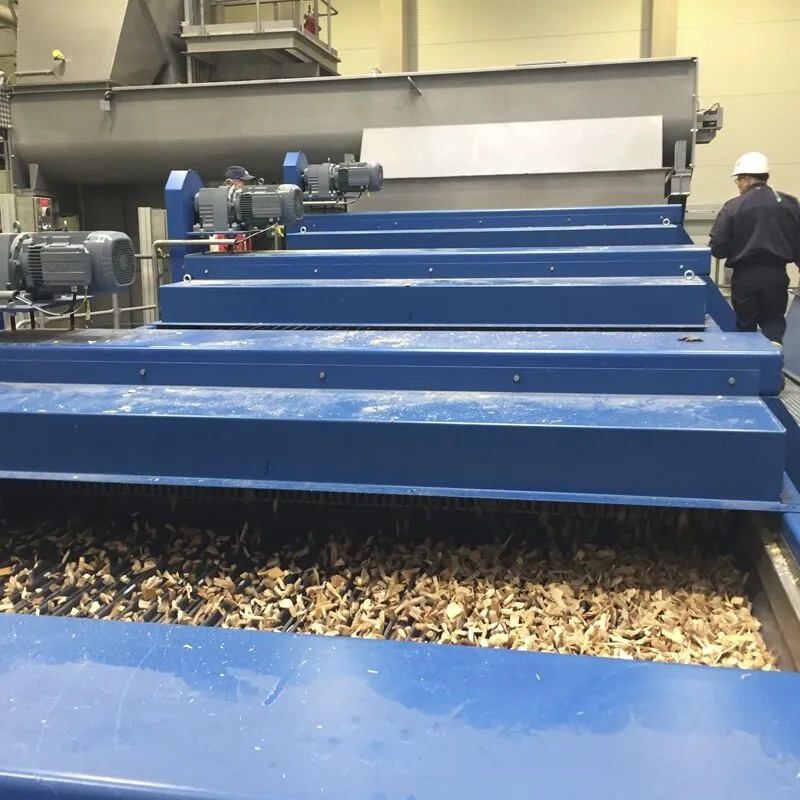
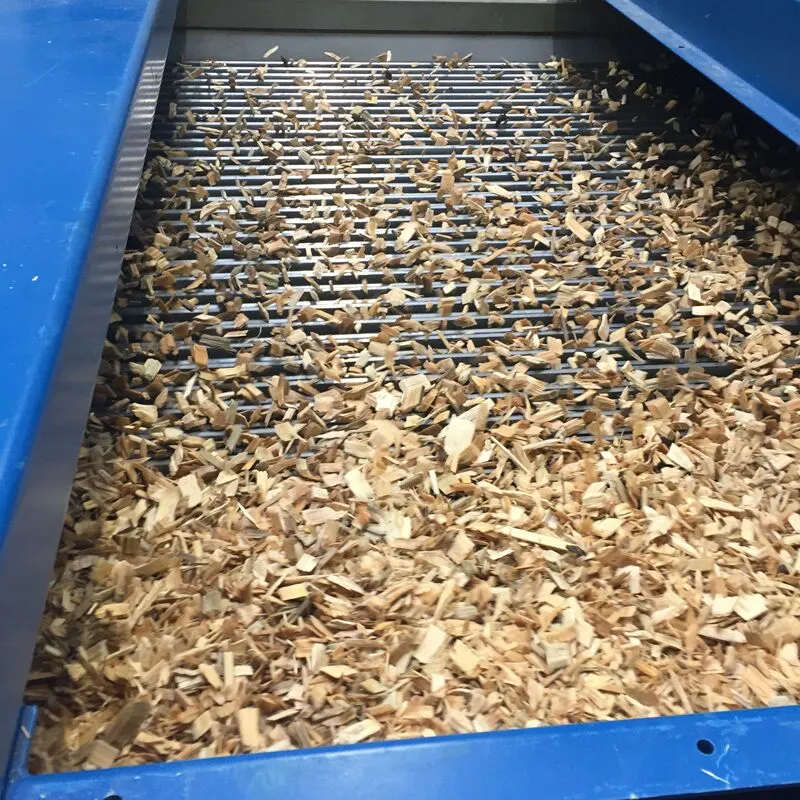
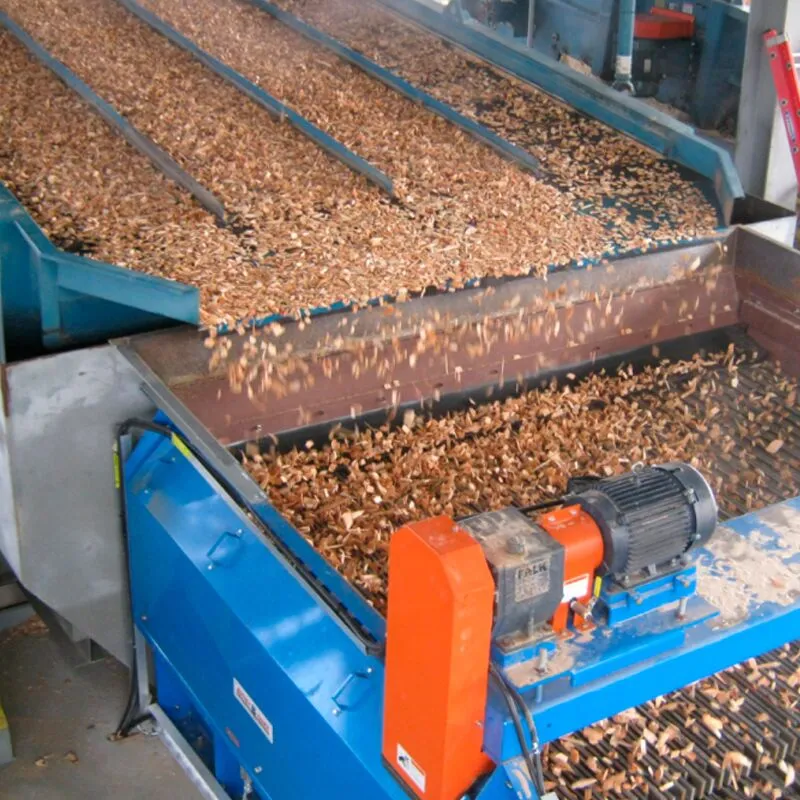
Features and Benefits:
- Better Selectivity: Superior selectivity ensures only acceptable-sized chips pass through while retaining over-thick material.
- Greater Flow-Rate Control: Precise control over a wide range of flow rates enables efficient chip screening at varying production speeds.
- Energy Efficiency: Low horsepower requirement for high throughput results in substantial energy cost savings.
- Space Efficiency: Compact, flexible footprint reduces space requirements in screen rooms, suitable for new and existing operations.
- Low Maintenance: Elimination of rotating wear surfaces reduces maintenance costs and extends screening surface performance life.
- High Separation Efficiency: Achieves over 90% separation efficiency for high-quality chip screening.
- Low Accept Carryover: Maintains excellent screening performance with accept carryover under 10% even at varying flow rates.
- Long Wear Life: Gentle oscillating action leads to significantly longer wear life compared to conventional screens.
- Cost-Effective Replacement: Sections of the screening surface can be replaced without removing shafts, minimizing downtime and costs.
- Versatile Installation: Suitable for both new installations and existing operations, offering a cost-effective primary screening solution.
- Technological Advancements: Innovative design with preset and locked steel bars for superior chip screening performance.
- Enhanced Fiber Quality: Improved screening efficiency contributes to better pulping benefits and enhances fiber quality.
- Variable Speed Operation: Independently driven modules allow for variable oscillation speeds to meet specific performance objectives.
- Flexi-Dek Material: Utilizes noncorrosive, high-density, high-strength Flexi-Dek material for flexibility and long wear life.
- Elimination of Rotating Nip Points: Design eliminates rotating nip points, reducing wear and maintenance concerns.
- Cost-Efficient Installation: Low profile, low vibration levels, and low energy requirements make installation easy without complicated support structures.
- Primary Screening Solution: Eliminates the need for pre-thickness screening with gyratories or disc screens, reducing operational costs.
- Operational Flexibility: Adjustments in bar spacing and module speed provide operational flexibility without affecting separation efficiency.
- Even Material Distribution: Achieves maximum efficiency through even material distribution across the screen.
- Clearing in Normal Shutdown: Control system can clear material from the screen during a normal shutdown sequence.
- Capacity: Screening capacity depends on chip thickness distribution, ensuring effective screening for various chip sizes.
- Better Selectivity: Superior selectivity ensures only acceptable-sized chips pass through while retaining over-thick material.
- Greater Flow-Rate Control: Precise control over a wide range of flow rates enables efficient chip screening at varying production speeds.
- Energy Efficiency: Low horsepower requirement for high throughput results in substantial energy cost savings.
- Space Efficiency: Compact, flexible footprint reduces space requirements in screen rooms, suitable for new and existing operations.
- Low Maintenance: Elimination of rotating wear surfaces reduces maintenance costs and extends screening surface performance life.
- High Separation Efficiency: Achieves over 90% separation efficiency for high-quality chip screening.
- Low Accept Carryover: Maintains excellent screening performance with accept carryover under 10% even at varying flow rates.
- Long Wear Life: Gentle oscillating action leads to significantly longer wear life compared to conventional screens.
- Cost-Effective Replacement: Sections of the screening surface can be replaced without removing shafts, minimizing downtime and costs.
- Versatile Installation: Suitable for both new installations and existing operations, offering a cost-effective primary screening solution.
- Technological Advancements: Innovative design with preset and locked steel bars for superior chip screening performance.
- Enhanced Fiber Quality: Improved screening efficiency contributes to better pulping benefits and enhances fiber quality.
- Variable Speed Operation: Independently driven modules allow for variable oscillation speeds to meet specific performance objectives.
- Flexi-Dek Material: Utilizes noncorrosive, high-density, high-strength Flexi-Dek material for flexibility and long wear life.
- Elimination of Rotating Nip Points: Design eliminates rotating nip points, reducing wear and maintenance concerns.
- Cost-Efficient Installation: Low profile, low vibration levels, and low energy requirements make installation easy without complicated support structures.
- Primary Screening Solution: Eliminates the need for pre-thickness screening with gyratories or disc screens, reducing operational costs.
- Operational Flexibility: Adjustments in bar spacing and module speed provide operational flexibility without affecting separation efficiency.
- Even Material Distribution: Achieves maximum efficiency through even material distribution across the screen.
- Clearing in Normal Shutdown: Control system can clear material from the screen during a normal shutdown sequence.
- Capacity: Screening capacity depends on chip thickness distribution, ensuring effective screening for various chip sizes.